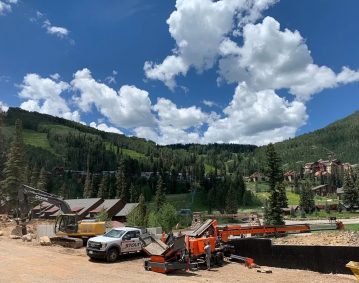
Material handling equipment is one of the most important factors in how operations proceed safely and efficiently in industrial production. Correct selection, installation, and service of material handling systems have a direct impact on reducing downtime and increasing overall production. Through the optimization of processes, these systems have the potential to enable smoother process operation, shorten time to market, and increase manufacturing or distribution efficiency.
Importance of Material Handling Systems in Modern Industries
In the modern industry, ranging from manufacturing to warehousing, material handling equipment plays a critical role in transporting, storing, managing, and safeguarding materials during the manufacturing process.
Streamlining Material Movement Across Facilities
One of the most important benefits of material handling equipment is the capability to move materials rapidly and safely. Conveyor systems, for example, offer a continuous way of moving goods from workstation to workstation, storage facility, and shipping stations. In contrast to manual transportation, which is slow and subject to human error, these systems provide reliable and accurate transport of goods, accelerating and reducing effort.
Advanced conveyor manufacturers now produce systems equipped with features like variable speed controls, sensors, and automated stops. These enhancements enable companies to tailor the rate of operation to production needs such that the workflow never needs to slow down or become disrupted.
Reducing Bottlenecks and Delays
Blockages are frequent due to the buildup of materials in particular locations along the production line due to errors in process or equipment shortages. Material handling solutions are designed to eliminate such disruptions. Automated systems can continuously move products without stopping, ensuring that no single area becomes overloaded. For example, conveyor systems integrated with sorting technology can automatically direct materials to their appropriate destinations, avoiding unnecessary delays. Further, industrial conveyor systems can be configured to operate at a wide range of sizes and weights, thus being highly modular to adapt to different functional requirements.
Enhancing Coordination Between Processes
Material handling equipment promotes better integration of different production and logistics phases. Many automated material handling systems are fitted with tracking and monitoring systems, and companies can monitor the movement of goods in real-time. This view guarantees that each workflow step is compatible with the production schedule. These systems can be used with warehouse management software to deliver inventory level updates, shipment status updates, and order progress status updates. That synchronization lessens misunderstandings and ensures that all the departments work together to increase the efficiency of the workflow.
Supporting Customization for Specialized Needs
There are particular needs in each industry for the treatment of materials. Supply needs are met by conveyor manufacturers with customized solutions, from handling delicate goods to high-speed production lines or heavy applications, etc. Custom material handling systems have characteristics that will be size, weight capacity, and environmental conditions specified to adapt the system to give optimum utilization. For example, food processing plants will have conveyors with stainless surfaces to meet hygiene levels, and automotive manufacturers will need heavy-duty conveyors to transport significant components, etc. Custom material handling solutions can enable companies to improve their workflow to meet these unique needs.
Increasing Output Through Automation
Automation is one of the major contributors to improving the efficiency of current material handling systems. Substitution of manual work tasks by automated machinery not only shortens processing time but also guarantees a good repeatability of results. Automated industrial conveyor systems, for instance, can operate continuously without fatigue, handling large volumes of goods around the clock. Additionally, automation reduces errors caused by manual handling, such as misplaced items or damaged products. Using consistent quality and quantity, these systems enable companies to comply with tight timetables and enhance customer satisfaction.
Improving Space Utilization
Material handling equipment for conveyor maintenance also excels in the efficient utilization of real space available. Conventional manual handling has the drawback of requiring a location large enough for workers to move around freely, which inevitably creates dead space. Material handling solutions like vertical storage systems and compact conveyors maximize the use of limited floor space. Conveyor manufacturers design systems that can be installed at various levels, including overhead, freeing up valuable floor space for other operations. This enhanced configuration optimizes the layout, improving workflow by providing a more structured, effective, and organized workspace.
Supporting Scalability for Growing Operations
The more their enterprise grows, the greater the need for material handling. Material handling systems are built for scalability so companies can integrate new systems, or upgrade existing ones as production needs grow. As an example, conveyor suppliers commonly provide modular systems that are expandable or flexible to handle greater quantities of goods. This scalability ensures that businesses can maintain workflow efficiency even as they grow, avoiding the need for complete overhauls or additional downtime.
Conclusion
Material handling equipment is the game-changer in reducing downtime and improving productivity. Developed from conveyors to automated storage systems, these systems provide the support to maintain the material throughput throughout the production cycle. Continuing operational efficiency can be achieved by regular conveyor maintenance, as well as by intelligently combining material handling solutions. With the continued development of industries, the need to invest in stable material handling systems is obvious.